Bellow
Hardcore MB Enthusiast
Does anyone know how to go about ascertaining the roll centre height of a Rover P6's front suspension?
I already know the answer (7'' above ground level) but not the method. Is the (leading) top arm/wishbone viewed as a conventional wishbone of infinite length?
I already know the answer (7'' above ground level) but not the method. Is the (leading) top arm/wishbone viewed as a conventional wishbone of infinite length?
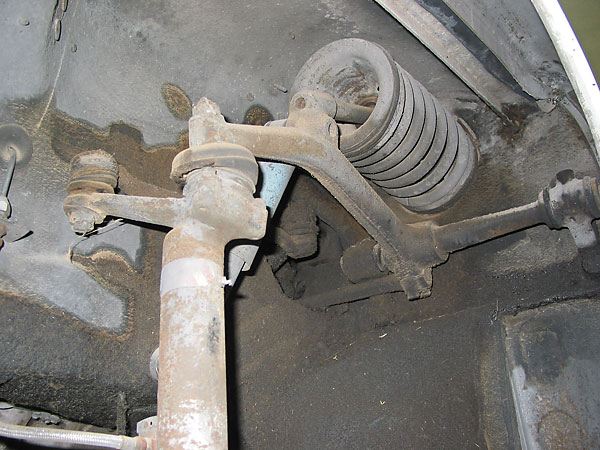