- Joined
- May 17, 2010
- Messages
- 3,557
- Car
- CLK5.6TT (WIP)
Thanks for the kind words guys.
With the exhaust manifolds ready, the next thing I wanted to sort out was the exhaust itself. This was also a DIY and took a few good weeks to finish. The manifolds were made out of mandrel bends which I had bent for me locally. For the exhaust I went with popular AMG 70mm pipe which isn't easily available in the UK. I found a supplier in Germany and placed an order for a number of bends that I'd calculated the new exhaust would require. As the parts were on their way to the UK, I've addressed a pair of Brabus boxes that I bought together with the Brabus bodykit to go on the car. The boxes were for E230-500 models and had smaller diameter pipes going to them. I wasn't sure if the piping is any bigger inside and decided to open and refabricated the boxes.
The boxes were welded around the perimeter so I carefully opened them up at both ends with a grinder:
And slid the shell off. Inside was a perforated pipe of a smaller diameter wrapped in wire wool, heat blanket and stuffed with sound insulation material:
I continued to take them apart by cutting the restricting end pipes off:
Then I measured, cut and welded a bigger perforated pipe as well as the ends instead of the originals used by Brabus (or Remus rather):
Wrapped in wire wool:
And welded it all up same as before:
With the exhaust manifolds ready, the next thing I wanted to sort out was the exhaust itself. This was also a DIY and took a few good weeks to finish. The manifolds were made out of mandrel bends which I had bent for me locally. For the exhaust I went with popular AMG 70mm pipe which isn't easily available in the UK. I found a supplier in Germany and placed an order for a number of bends that I'd calculated the new exhaust would require. As the parts were on their way to the UK, I've addressed a pair of Brabus boxes that I bought together with the Brabus bodykit to go on the car. The boxes were for E230-500 models and had smaller diameter pipes going to them. I wasn't sure if the piping is any bigger inside and decided to open and refabricated the boxes.
The boxes were welded around the perimeter so I carefully opened them up at both ends with a grinder:
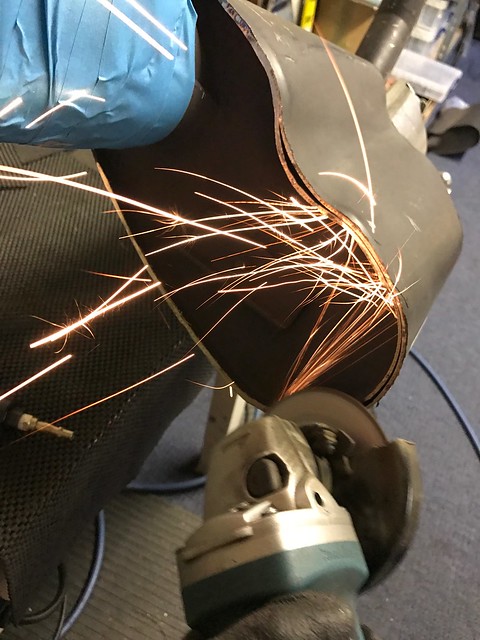
And slid the shell off. Inside was a perforated pipe of a smaller diameter wrapped in wire wool, heat blanket and stuffed with sound insulation material:
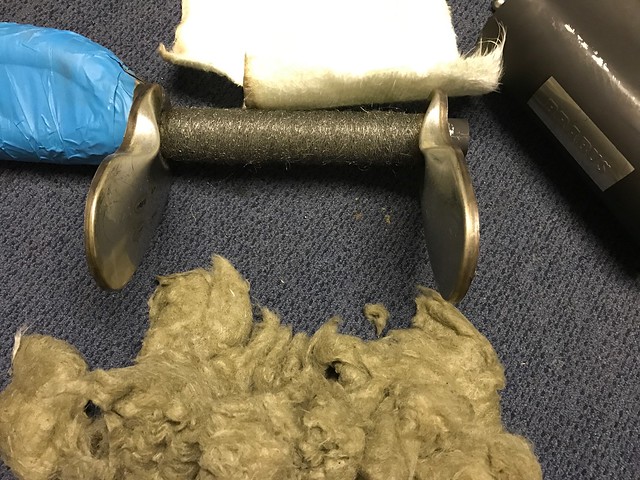
I continued to take them apart by cutting the restricting end pipes off:
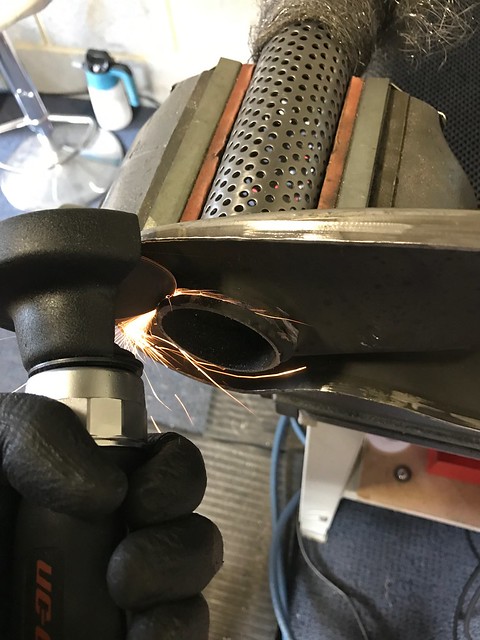
Then I measured, cut and welded a bigger perforated pipe as well as the ends instead of the originals used by Brabus (or Remus rather):
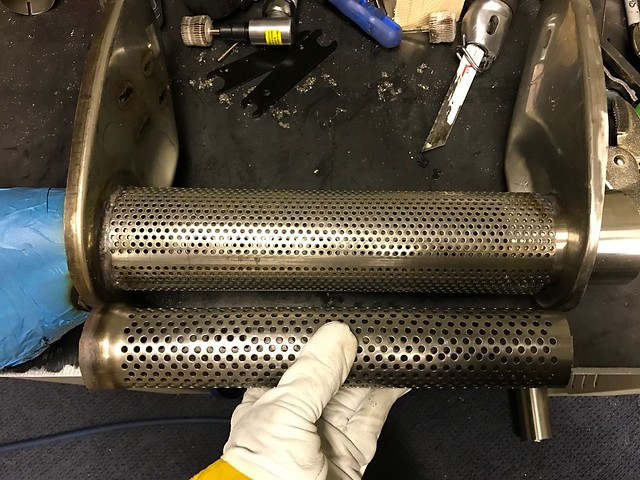
Wrapped in wire wool:
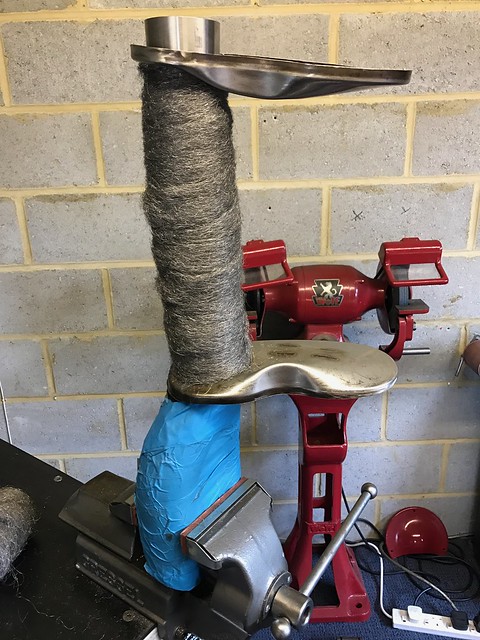
And welded it all up same as before:
