Finally, I have got round to doing a pukka fix for the W202 (facelift) wiper. It took approx 6 hours over xmas in my Dads workshop. This was good because my Dad was there to help (read 'does most of the work) AND he gets to try out his new lathe...
Firstly, remove the wiper from the car and strip it back so that you are left with just this bit.
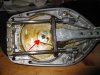
Now remove the guides, you need a torx screwdriver.
Then you need to push the pin (arrowed) out of the plated steel arm. There are potentially two ways you can do this.
1) Drill the centre and it will tap out very easily with a punch
2) You could press it out
We chose the former, we discovered the viability of option 2 after we had removed the pin. When drilling it out we started with a 2mm drill (to keep everything central) and slowly worked up to a 7.5mm drill, it tapped out very easily. You could prob get away with 7mm as 7.5mm was pretty close.
It turns out that the pin is splined inside the plated steel (I tried to put a pic up of the old shaft but couldn't, limited to three pics).
We then separated the old pin from the gear by pressing it out. The old gear appears to be made of nylon or similar and looks like it was also pressed onto the shaft. Given that it is made of nylon and splined it’s no surprise that it fails if you don’t grease the mechanism!
So, on the lathe we made a new pin. 10mm diameter (to fit inside the bush and hold the gear) with an 8mm diameter to go through the plated arm. Length of the 10mm section of the pin was 31.59mm and the length of the 8mm diameter end was 3.75mm (plated arm is 3.55mm thick). Both ends of the shaft were machined to be a “press fit” which is up-to ½ a thousandth oversize (force fit is up-to 1 thou oversize). The middle bit was polished a bit longer to ensure it runs smoothly in the bush, the groove in the middle was a bit of a guess to come close-ish to the original.
At this point I should mention that my Dad works in imperial most of the time hence the metriperial units…..
Anyways, the arm was drilled in the end to approx 1.5mm (actually something imperial), approx half the arm thickness so that it could be pinned (making splines is not easy). We did this with a pillar drill and had everything set-up vertically and clamped in place to ensure the drill went straight through as it is easy to get such a small drill to drift off-line.
With the arm drilled, the pin was pressed in, back in the drill to drill the pin too, this was then pinned with a roll pin (a very hard one, and a very snug fit) which was punched in. This leaves you looking like this (old gear and pin in the picture for reference).
- Pic of new gear (far left)
- new pin (left centre) inserted into rotor arm and pinned in place
- old pin (centre right), spline to connect to gear at the bottom, splined to fit the rotor arm at the top
- on the far right is the old gear.
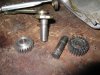
The new gear in the picture is a steel one, it has a lip on one side as that is how it came, we turned it down in the lathe to a thickness of 10.5mm, same as the original (the teeth on the new gear are only 8mm thick, that’s just how they come). The bore of the gear is 10mm. The teeth are identical to the original.
Grease the pin and assemble the arm/pin through the bush in the housing. Remember to install all the washers too, there is one between the arm and the bush and one between the gear (underside and the bush).
Clean the pin of grease where it comes out of the bottom (we used acetone), put loctite inside the gear and fit the gear. Once the loctite has set, drill between the gear and pin. We drilled big enough to allow us to tap for countersunk 6BA screw. I didn’t loctite the screw but we did dot-punch it in place. And voila......
Picture of re-built assembly with new gear and locking screw.
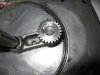
Re-build everything that you removed (guides etc). Re-assemble the wiper, remember to grease everything, remember that the wiper is at its shortest when vertical so set the wiper vertically then turn it till the marks on the back match up, THEN connect the drive mechanism. This ensures it wipes symmetrically (I didn’t and had it shortest at the mark point so it wiped slightly odd and had to re-assemble. It now works a treat and is perfectly quiet when it operates.
I hope people find this useful and it all makes sense, I wasn’t too great at taking pictures but anyone who has already stripped one of these should be reasonably familiar. I’m happy to answer any questions if there are any, cheers, Chris
Firstly, remove the wiper from the car and strip it back so that you are left with just this bit.
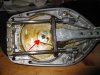
Now remove the guides, you need a torx screwdriver.
Then you need to push the pin (arrowed) out of the plated steel arm. There are potentially two ways you can do this.
1) Drill the centre and it will tap out very easily with a punch
2) You could press it out
We chose the former, we discovered the viability of option 2 after we had removed the pin. When drilling it out we started with a 2mm drill (to keep everything central) and slowly worked up to a 7.5mm drill, it tapped out very easily. You could prob get away with 7mm as 7.5mm was pretty close.
It turns out that the pin is splined inside the plated steel (I tried to put a pic up of the old shaft but couldn't, limited to three pics).
We then separated the old pin from the gear by pressing it out. The old gear appears to be made of nylon or similar and looks like it was also pressed onto the shaft. Given that it is made of nylon and splined it’s no surprise that it fails if you don’t grease the mechanism!
So, on the lathe we made a new pin. 10mm diameter (to fit inside the bush and hold the gear) with an 8mm diameter to go through the plated arm. Length of the 10mm section of the pin was 31.59mm and the length of the 8mm diameter end was 3.75mm (plated arm is 3.55mm thick). Both ends of the shaft were machined to be a “press fit” which is up-to ½ a thousandth oversize (force fit is up-to 1 thou oversize). The middle bit was polished a bit longer to ensure it runs smoothly in the bush, the groove in the middle was a bit of a guess to come close-ish to the original.
At this point I should mention that my Dad works in imperial most of the time hence the metriperial units…..
Anyways, the arm was drilled in the end to approx 1.5mm (actually something imperial), approx half the arm thickness so that it could be pinned (making splines is not easy). We did this with a pillar drill and had everything set-up vertically and clamped in place to ensure the drill went straight through as it is easy to get such a small drill to drift off-line.
With the arm drilled, the pin was pressed in, back in the drill to drill the pin too, this was then pinned with a roll pin (a very hard one, and a very snug fit) which was punched in. This leaves you looking like this (old gear and pin in the picture for reference).
- Pic of new gear (far left)
- new pin (left centre) inserted into rotor arm and pinned in place
- old pin (centre right), spline to connect to gear at the bottom, splined to fit the rotor arm at the top
- on the far right is the old gear.
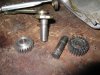
The new gear in the picture is a steel one, it has a lip on one side as that is how it came, we turned it down in the lathe to a thickness of 10.5mm, same as the original (the teeth on the new gear are only 8mm thick, that’s just how they come). The bore of the gear is 10mm. The teeth are identical to the original.
Grease the pin and assemble the arm/pin through the bush in the housing. Remember to install all the washers too, there is one between the arm and the bush and one between the gear (underside and the bush).
Clean the pin of grease where it comes out of the bottom (we used acetone), put loctite inside the gear and fit the gear. Once the loctite has set, drill between the gear and pin. We drilled big enough to allow us to tap for countersunk 6BA screw. I didn’t loctite the screw but we did dot-punch it in place. And voila......
Picture of re-built assembly with new gear and locking screw.
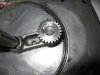
Re-build everything that you removed (guides etc). Re-assemble the wiper, remember to grease everything, remember that the wiper is at its shortest when vertical so set the wiper vertically then turn it till the marks on the back match up, THEN connect the drive mechanism. This ensures it wipes symmetrically (I didn’t and had it shortest at the mark point so it wiped slightly odd and had to re-assemble. It now works a treat and is perfectly quiet when it operates.
I hope people find this useful and it all makes sense, I wasn’t too great at taking pictures but anyone who has already stripped one of these should be reasonably familiar. I’m happy to answer any questions if there are any, cheers, Chris