Sp!ke
Administrator
So yesterday I had my winter tyres fitted on the 201 and on the way home I started getting a horrible noise coming from the front O/S.
It sounded like a rubbery graunchy sort of noise when turning the steering wheel. Initially I thought it was a tyre rubbing but concluded that it couldn't be because it made the noise at standstill.
On closer inspection I'm pretty sure its the lower ball joint making the noise. Not sure how changing a wheel could have encouraged it to fail all of a sudden but maybe jacking the car up on the wishbone or something has prompted its rapid demise.
Anyway, I'd better change the ball joint sharpish I guess and in the interest of keeping costs down I'm intending to only change the ball joint itself rather than the whole wishbone. So I need to add to my tool collection and purchase an appropriate tool to press the balljoint out of the wishbone.
So, does anyone know if this press below is suitable?
Ball Joint Service Removal Separator 4x4 Adaptors on eBay (end time 26-Nov-10 14:32:31 GMT)
It sounded like a rubbery graunchy sort of noise when turning the steering wheel. Initially I thought it was a tyre rubbing but concluded that it couldn't be because it made the noise at standstill.
On closer inspection I'm pretty sure its the lower ball joint making the noise. Not sure how changing a wheel could have encouraged it to fail all of a sudden but maybe jacking the car up on the wishbone or something has prompted its rapid demise.
Anyway, I'd better change the ball joint sharpish I guess and in the interest of keeping costs down I'm intending to only change the ball joint itself rather than the whole wishbone. So I need to add to my tool collection and purchase an appropriate tool to press the balljoint out of the wishbone.
So, does anyone know if this press below is suitable?
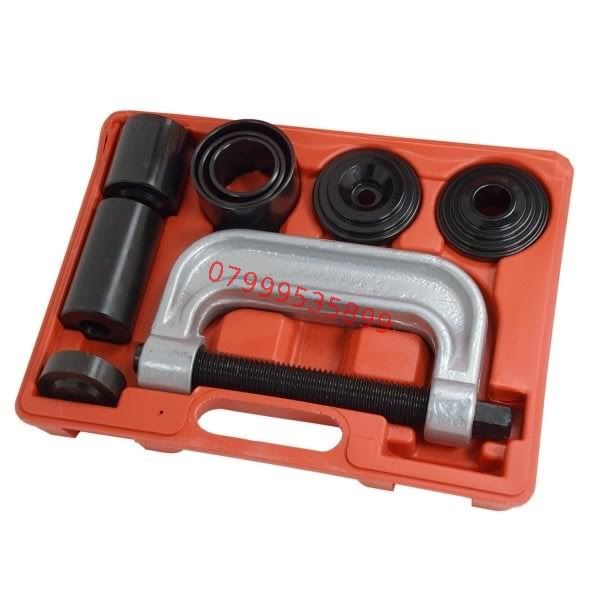
Ball Joint Service Removal Separator 4x4 Adaptors on eBay (end time 26-Nov-10 14:32:31 GMT)
Last edited: